PRESS | 01 SEPTEMBER 2022
Jumbo Offshore installs Petrobras torpedo pile mooring system.
Jumbo Offshore completes another first by installing Petrobras torpedo pile mooring system with just one vessel
Adding to its list of ‘milestone’ projects, Jumbo Offshore has executed the transport and installation of a torpedo pile mooring system, including mooring for flexible risers, umbilical for Libra Consortiums “Guanabara” FPSO. While this type of installation previously required the mobilisation of up to three anchor handling tugs, Jumbo carried out the entire contract using only its J-class offshore installation vessel Fairplayer, working in the Mero field of Brazil’s Santos Basin.
Libra Consortium is operated by Petrobras (38.6%), in partnership with Shell Brasil (19.3%), TotalEnergies (19.3%), CNPC (9.65%) and CNOOC (9.65%) and Pré-Sal Petróleo SA (PPSA) (3.5%), representing the Government in the non-contracted area.
Jumbo started investigating this with the ambition to offer a more efficient and sustainable installation method. “Our first studies into a workable solution started around 2010,” says Brian Boutkan, Jumbo Head of Sales and Business Development, Americas.
Jumbo carried out the project in Q1, Q2, Q3 and Q4 2021; its scope of work consisted of the installation of 24 120-tonne torpedo anchor piles and connecting chains and polyline sections, and the installation of 11 35-tonne anchors for the flexible risers and umbilical mooring lines. The work also included the preliminary survey of the seabed and the removal of obstacles, and post-lay survey.
The torpedo mooring system is a Petrobras in-house developed method of mooring large floating structures such as FPSOs. The installation process involved lowering the torpedo pile to a set depth above the seabed. It is then released, free-falling at high speed through the water before penetrating the seabed. An ROV is then deployed to attach mooring chains and lines. Up until Jumbo’s one-installation-vessel method, this procedure has usually been performed by two anchor handling vessels working in tandem, sometimes even with a third vessel performing the ROV monitoring and survey work.
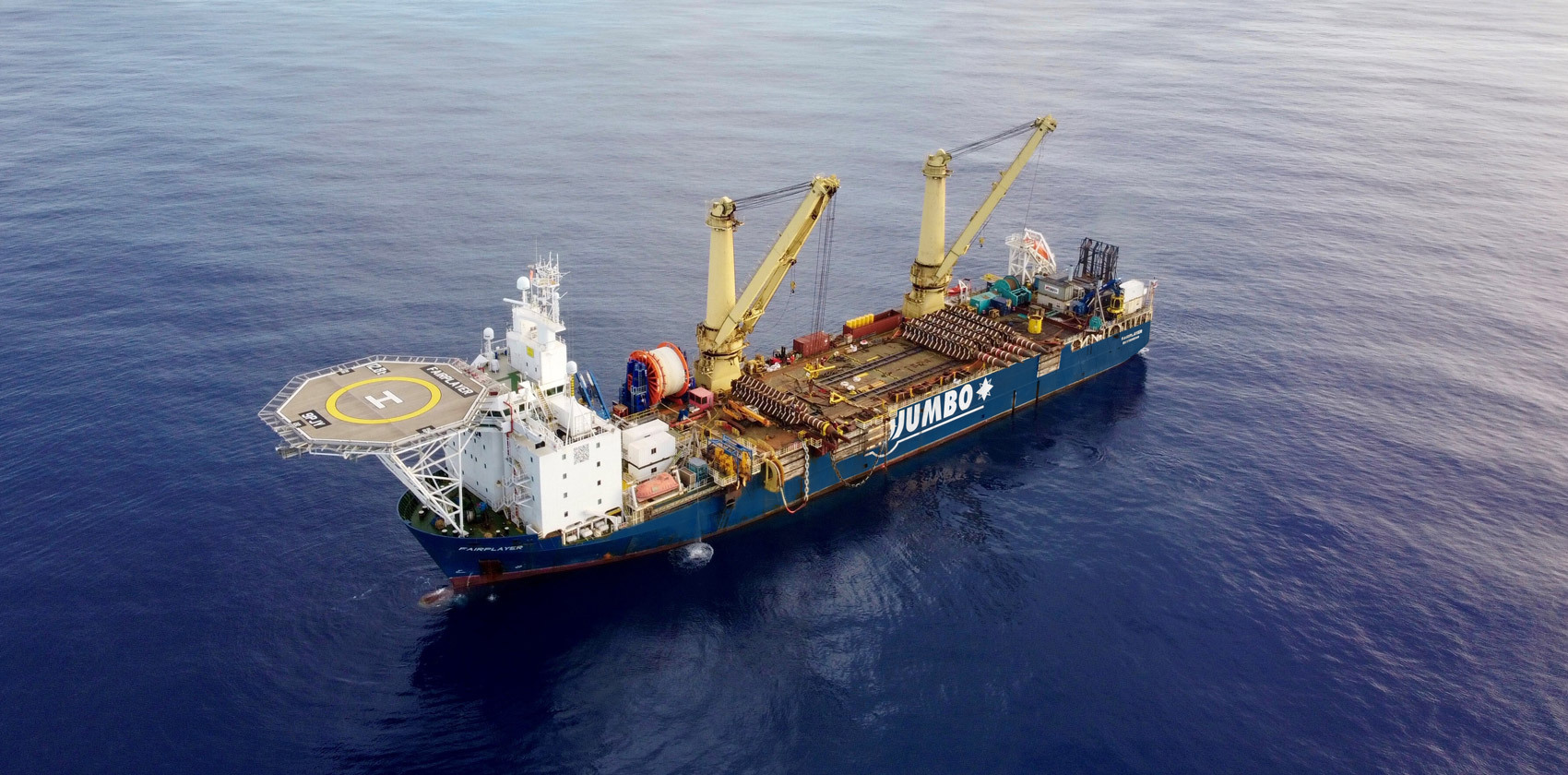
Jumbo Fairplayer
Tilt, lower and launch methods
The Fairplayer started the project with the 120-tonne piles, using one of its two 900-tonne cranes to tilt them over the side of the vessel, and then winch them down to the ‘launch’ depth.
After a final location check, the torpedo could be released to freefall to the seabed. “Working with one vessel enabled a much more controlled process,” Boutkan notes. “Furthermore, compared to previous campaigns with anchor handling vessels, the operations at the port were also more efficient. The Fairplayer has its own cranes, which meant we could pick up the equipment ourselves. And she has a large deck, so she carried more torpedos and needed less trips to port.”
Offshore conditions
Repeating this process 24 times, Jumbo’s crew increased its workability and efficiency in the installation process. “There are always waves and swell when working in the South Atlantic region offshore Brazil. During the installation we encoutered all seasons, from summer to winter. This definitely gave us some challenges, but we improved our efficiency in working with the piles to a point that we could install them even in higher waves.”
The project progressed with the installation of the smaller 35-tonne anchor piles. Although these required a slightly different installation method, Jumbo had the flexibility to make the necessary changes to provide a comprehensive mooring installation package that included the flexible riser and umbilical anchors.
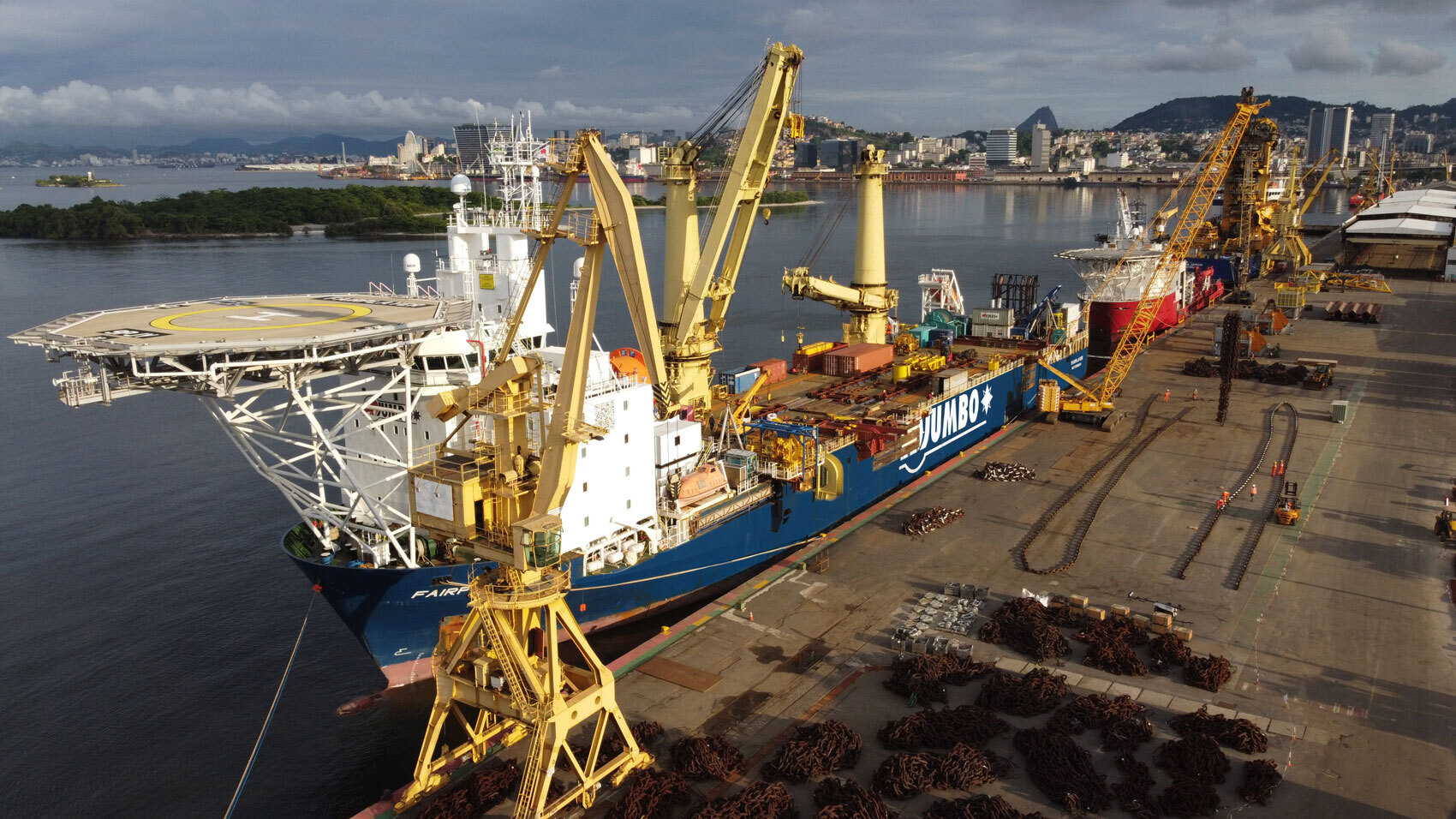
Port of Santos, Brazil
Project delivery without a twist
The project concluded with the mooring line installation campaign. The mooring lines consisted of both chain and polyester segments, so Jumbo needed two separate overboarding systems. Boutkan explains: “After attaching the mooring line to the pile, we laid the chain and remainder of the mooring line in a predetermined corridor on the seabed. It’s important not to have too many twists in the line, so we checked this by flying over the installed mooring with the ROV.”
Looking back at the recently completed contract, Jumbo project manager Rick Bruinsma highlights the key factors in the project’s success. “The inventiveness of the engineering team, together with a successful continuous improvement program involving all disciplines, led to reduced installation cycle times throughout the whole offshore campaign. Furthermore, our constant focus on safety resulted in zero LTIs. And this whole operation was COVID-free – the health of the crew was assured and the project was not hampered or interrupted by COVID during the installation campaign. For that our project team, crewing and operations departments deserve a huge compliment for keeping everything going.”
Related news
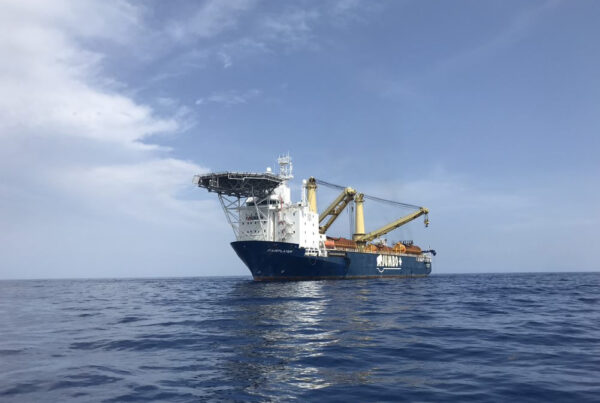